The first in the list of chores was to check the vehicle and all of its equipment off at the beginning of a shift. In theory, this involved carrying out a detailed inspection of all of the vehicles inventory against a check-list of what was supposed to be there.
Every single item was supposed to be counted to ensure minimum numbers of the items were present according to the list. Most consumable items were stored in plastic containers in the long cupboards above the stretchers. One container might have four different sizes of bandages, another dressings, oxygen masks, tubes etc.
There were also the jump kits which contained most of the important gear that would be taken to the patient. These would hold drugs, bandages, dressings, oxygen, masks, IV gear etc.
Each drug in these would have to be counted and the expiry date checked. The oxygen and entonox gas levels in the kits and vehicle were inspected, recorded and replaced if required.
The other equipment including the stretchers, splints, linen and ECG defibrillator / monitor (defib for short) was checked and tested.
Even the vehicle itself was examined. The brake lights, indicators and head and taillights were checked. The beacons, siren and horn were also tested, as was the oil and water levels.
I always made sure the vehicle was ready to go and that I had enough pillows and linen, particularly on a cold day or night. Pillows make great splints so it was important that I had at least three.
In reality, when it came to checking the vehicle off most staff got to know what was supposed to be in the vehicle and a quick once over of the items was usually the standard approach.
As the reader can imagine the routine can be boringly repetitive after doing the same thing every shift, every day, every year. Consequently some staff became very complacent and a few didn’t even bother carrying it out much at all. This of course was potential for disaster.
There was once just such a lax crew who started their shift at one of the quieter stations and asked the previous crew if everything was in place to which they replied it was. The new crew took the previous crews word that everything was accounted for and obviously didn’t bother to do a check themselves. The trouble was that the previous crew also hadn’t checked the vehicle off properly at the start of their shift and didn’t do any jobs that would have required them to re-stock any items.
Unfortunately the new crews first job was being responded to a cardiac arrest and on arrival a shocked and panicky crew discovered there were no batteries in the defibrillator! They had been removed for charging and not been replaced and the crew had not checked the equipment. They had to call for another ambulance to back them up so the patient could be defibrillated.
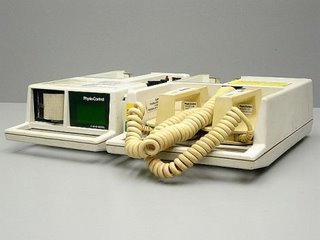
Needless to say such an action was extremely negligent and so they were counselled by the manager of the day. Thanks to backup from the union both crews were very lucky not to lose their jobs.
When the service had the Bedford and Chevrolet ambulances it was routine to remove the stretchers and mop the floor out at the end of each shift. The stretchers were often left out of the vehicle during the crew changeover so the floor could dry sufficiently.
This lead to an embarrassing moment for one poor crew who got called to an urgent job as soon as they arrived for work. The back doors were already closed so they jumped in and raced off to the motor vehicle accident they had been responded to.
Imagine their shock when they opened the back doors to get the stretcher out only to find there were none! A sheepish crew had to call for a backup vehicle to transport the patient and return to station to retrieve their stretchers.
No comments:
Post a Comment